N-connectors - good
element, but do not buy fakes...
For people working in telecommunications, it is known that
approximately 90% of the malfunctions of the telecommunication technology
sets are caused by faulty connectors. However, the general term "defective
connectors" means not only poor quality connectors, but also poor quality
connections, or poor quality connectors due to the wrong connector
+ cable pair was selected. Not
surprisingly, telecommunications companies are sacrificing so much finance
and organizational effort to train technicians and select the appropriate
components. If we leave aside historical so-called UHF connectors (which
are not UHFs at all) of type PL259 and SO239, which actually are not,
because they do not meet the basic premise of RF coaxial connectors - ie
repeated assurance of nominal impedance - and BNC, N, and SMA connectors
are by far the most widespread among radio amateurs aware of the technical
context. These connectors cover the most commonly used radio frequency
bands up to (albeit with some compromises) up to 24GHz and are capable
carry of transmitting power up to 1kW (on lower frequency bands up to
1GHz). While BNC connectors are very often available on the market today
as very cheap and therefore usually a poor quality substitute for other
professional connectors (leading to their poor quality and endless
manifestations of different bags), radio amateurs often reject them and
have gained great popularity with SMA connectors. with the undesirable
manifestations significantly better. However, their design is not designed
to transmit higher power (max 200W). Therefore, probably the most
widespread connectors on VHF bands today are type N connectors, which were
created during World War II in the US to connect the first radar systems
in the US Navy.
But: history and technical theory is one thing and today's commercial
world is another one. Although politicians shout out the phrase about the
digital omnipotence, life is still primarily analog. The connector
parameters are measured for conductivity, attenuation, impedance
mismatching, reliability and especially cost. And among radio amateurs,
few realize that the price is parameter number 1. and other parameters are
solved by some compromise - at a given price to meet the parameters of the
equipment, its reliability and transmission capacity - all of course for a
given project, which represents assemblies that need to be properly
mounted, connected and energized for the final assembly. But the
techno-economic life of the device is getting shorter and especially for
IP technology, it has now fallen from the original 10 years to half when
the device goes into scrap - not because it no longer works but because
the new device has a higher transmission capacity and other features - it
is not necessary to set anything on it, can work at a higher temperature,
consumes less electricity, etc., etc. Well, and the liquidated device,
which in his lifetime has never been disassembled and done nothing,
becomes a grateful source of material for amateur radio designers. Many
then believe that the connectors removed from such a device must be a
quality standard. It does not have to be. In addition, the situation will
deteriorate in the coming years, as all radio transmission devices are
moving to an antenna. You can use from it just a piece of waveguide
connected to some microstrip structure because the whole device is without
connectors - if we skip the matter of optical connectors connecting ODU
and data technology somewhere below the mast. Today, the industry has the
latest equipment, equipped with connectors, and in a few moments will have
to buy them in electronics stores. And unlike semiconductors, they will be
very expensive. This article therefore aims to introduce the amateur radio
community to what is important and what to watch out for N-type
connectors.
The brand is still a standard of quality! I will borrow the answer
from one TV contest: "yes, yeah ..." There are several traditional
manufacturers in Europe and the USA who simply produce 1A quality
connectors and it is their professional pride to leave high quality
connectors to the market - sure you know them and I would include Spinner,
Suhner, Rosenberger and Radiall. If you reach for them, they will serve
you for years without necessity to pay attention to them. Well, then there
are brands like Amphenol and Telegärtner. Also very sophisticated and
experienced connector manufacturers - but they are already on the order of
equipment manufacturer or market, able to produce connectors 1B quality,
because they are cheaper and certainly suited to the application ordered.
And then there is a whole host of other manufacturers. How do you
recognize the good ones? Simply - for the highest quality connectors, the
manufacturer usually does not hesitate to state their name or logo.
Incidentally - in Czechoslovakia were once manufactured connectors in
Mikrotechna belonged to the best quality, which could be obtained on the
market and had certificates for use in the civil aviation industry and
Army. Where are those times ...
Chinese connectors are a phenomenon of a time when European and
especially American economists moved production (and related know-how) to
Asia get a short-term savings without realizing it. that in doing so they
are liquidating the domestic industry in the medium term. So today you can
buy
top quality as well as 3rd quality in China. Be careful. There are
Chinese 1A quality connectors with the name and logo of the above
reputable manufacturers, but also fakes. You can find out what to watch
out for below.
Gold? The connector contacts are only covered with a microscopic
(if any) gold layer. However, the yellow color of the contacts tells
nothing about the quality of the connector. Above all, it is good to
realize that gold is soft and rubs. Therefore, the reputable manufacturers
are covered with various hard alloys of gold, silver, rhodium and other
metals with good conductivity. Gilded contacts made sense in the Czech
Republic when the North Bohemian coal-fired power plants spewed millions
of tons of sulfur dioxide into the atmosphere, causing silver to black.
Fortunately, the time is gone and the same (or better) service on the
contacts and silver, respectively. its alloys. Although I saw the answer
of a famous "guy" that gilded PL259 connectors go to 23cm ... hihi
Teflon? Another myth. The plastic in the connectors is usually
Teflon, but it does not have to be Teflon. Since many plastics have
similar dielectric (dielectric constant, voltage strength and delta
tangent dielectric loss) and mechanical parameters like PTFE at normal
temperatures, replacing Teflon with connector quality may not be an
obstacle - with one crucial exception: If the contacts are in plastic
("like a teflon only") internal parts of the connector anchored
permanently, cannot be soldered! And the contacts of high quality
connectors for medium and larger power are soldered! So if you have a
connector where you can remove individual plastic insulators from the
contacts and solder the contact separately to the cable, there is no
obstacle to using the such Teflon replacement, since you will not assemble
the connector parts until the parts have cooled down. However, if this is
not possible, avoid such a connector. Teflon in the connector has one more
feature. It has a high thermal expansion and if the connector heats up
when transmitting higher RF power, the Teflon exerts a pressure inside the
connector which leads to a reduction of clearances and thus transient
resistance. The same function in the connector is the rubber ring, which
maintains a constant pressure and thus small transition resistances at the
outer conductor of the coaxial cable. Take care: in the crimp connectors
such flexible element is not used, so rather reject the cable connector
that does not have a rubber ring.
Construction: it is tied to the respective cable. Never install a
connector on a cable that is not designed for that connector. Cables are
different, some time not very good ... A copper foil cable and a few hairs
with a tenth of mm diameter instead of shielding, of course, install
poorly into the connector. The connectors for such a cable (similar to
those for aluminum cables) have a tube in their design that must be
plugged into the cable (heat the cable sheath with a hairdryer). However,
if possible, for type N connectors, preferably use cables with a solid
(preferably) 100% braid of wires and if you want to minimize its
attenuation, then with a foil that can easily be aluminum (on a plastic
carrier), which is in mechanical resistance better than copper foil alone
(without plastic carrier), which is brittle and cracking. Therefore, I
recommend the RF400 cable and its equivalents for type N connectors. And
even though the N connector connector is presented as waterproof, don't
believe it! Water always enters the connector. Therefore, after assembly,
we recommend wrapping the connector joint with a self-curing rubber tape
and, for permanent assembly, add a suitable wax insulator coat.
Male and female? - this problem directly focused to gender is (as
in nature) one of the most important factors of good connector connection.
Generally today, there is no longer a problem with the incompatibility of
dimensions as 50 years ago. However, the connector itself is realized as
the insertion of the contact tip into the connector collet (tie, ferrule).
And if the connector collet is not permanently spring and flexible, there
is a problem with the connector wear. Do not break the head with the male
connector for N connectors. This is practically always OK, unless there is
a major problem in the connector (see above). In other words: cough on the
N connectors of the "male" type, the problem of connector connection
occurs in the vast majority of cases in the "female" female (female) and
the problem is called the collet of the N connector "female"type.
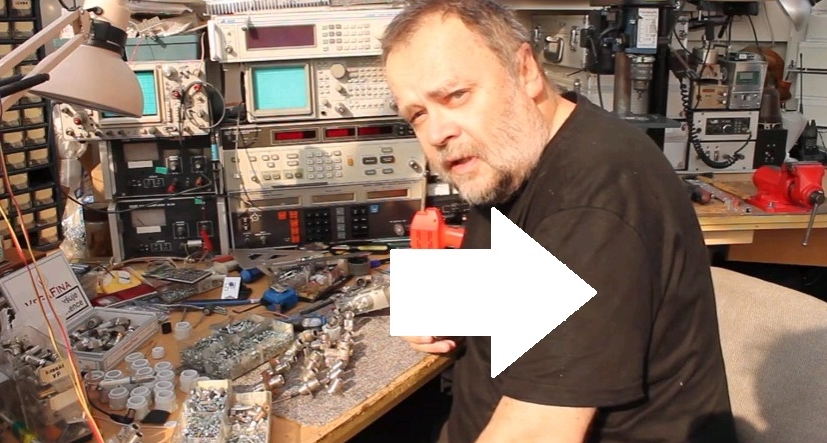
OK1VPZ video - click on to arrow
Materials and contacts (!): In
accordance with the above, an alloy must be used on the female connector
collet of the N connector to ensure permanent elasticity and not to
expand. See video. Such alloys are CuBe, or CuPbP in other words,
beryllium bronze, phosphor bronze, and somewhere Beryllium copper name can
be found. Spring collets are also labeled "spring contact" at some
manufacturers and who knows how. However, it is clear that ordinary
bronze, brass and similar materials do not have such flexibility and the
collet expands, resulting in poor contact, noise, intermodulation, or
overall loss of connection and burn out. And why aren't steel collets? It
is simple - see above - the metallization is easy to rub off and then the
conductivity of the material is decisive. And the steel is not exactly at
its best ... The collet of the female connector N is therefore an Alpha
and Omega quality connection! If you are buying connectors at a specialist
store, request a datasheet of the connector, if you are buying somewhere
in a flea market, take the pin removed from the male connector (dad)
soldered on it, insert the PIN into the collet of the connector you want
to buy, click a few millimeters to the right, left, up and down ... and
either the collet expands and do not buy such connectors, or the collet
stays tight and resilient, so you can hang two more such on the pin
inserted into the collet after such a test. connectors and pin will not
pull it out of the collet. Try it, it's easy! And remember: with a simple
glance you will not find out anything!
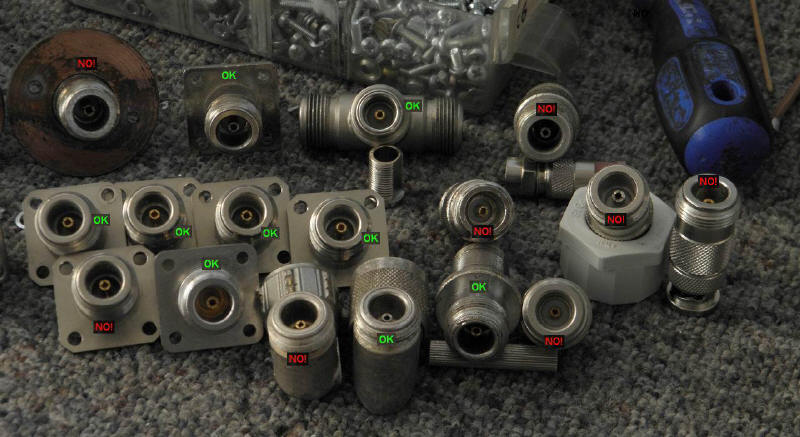
So that's more-less everything I wanted to tell you
about N-type connectors. And of course - the familiar saying is true: I'm
not so rich to buy cheap things! When you are at VHF contests, overhead a
large antenna system, which you have laboriously mounted and built in the
wind and rain, so saving the cost of one poor quality connector is not
worth a corrupt race ...
Well, and for final some pictures about the described test:
73 de OK1VPZ |